CNC Milling Machine
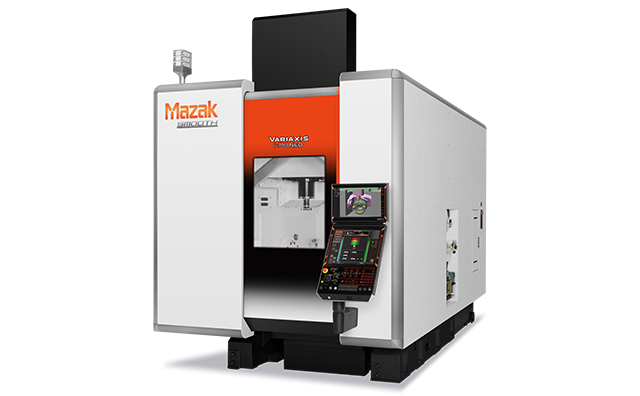
CNC Milling Machines and Their Versatile
Applications
A milling CNC machine is an essential tool in modern manufacturing, combining precision and efficiency to shape and refine materials with remarkable accuracy. Using computer numerical control (CNC) technology, these machines automate complex milling processes, producing consistent results in a fraction of the time required by traditional methods. They excel in crafting intricate designs, maintaining tight tolerances, and accommodating various materials, from metals to plastics. Reliable and versatile, a milling CNC machine is critical for industries like aerospace, automotive, and product prototyping, where quality and precision are paramount.
Unleash precision and efficiency with the Milling CNC Machine, your ultimate companion for high-performance machining. This machine is designed with cutting-edge technology and delivers flawless accuracy. It makes intricate designs.and detailed cuts effortless. Whether you’re crafting components for aerospace, automotive, or custom manufacturing, the Milling CNC Machine streamlines your workflow with advanced automation and lightning-fast operation. Its intuitive interface ensures ease of use, even for complex tasks, while its durable construction guarantees reliability for demanding projects. Achieve perfect results every time, while saving time, minimizing waste, and elevating your craftsmanship to new heights.
CNC Milling Machine Dealers in India
HEI is one of India’s leading CNC Milling Machine dealers and suppliers, known for our commitment to delivering high-quality machinery. We specialize in the import and export of advanced CNC machines that meet the evolving needs of modern industries. In addition to CNC Milling Machines, we also supply a wide range of industrial equipment, including Grinding Machines, Drill Tap Machines, Multi-Tasking Machine, and more. Our goal is to provide reliable and efficient solutions that boost productivity and performance across various manufacturing sectors.
Features of a Milling CNC Machine:
Automation in the realm of machining has revolutionized how we approach complex cutting paths, particularly with milling CNC machines. These advanced systems operate through meticulously pre-programmed software, enabling operators to achieve intricate designs with remarkable precision and efficiency. This integration of automation not only reduces human error but also enhances productivity by consistently executing complex tasks with unwavering accuracy. As these machines advance, they are increasingly equipped with adaptive algorithms that allow real-time adjustments during operation. This means a milling CNC machine can respond dynamically to variable material properties or unexpected tool wear without halting production—a game changer in high-volume manufacturing settings. Furthermore, the ability to store and replicate a multitude of cutting paths means businesses can seamlessly move from prototyping to mass production, accelerating time to market for new products and innovations. Embracing this technology not only optimizes existing processes but also paves the way for future advances in smart machinery, ultimately leading to a more efficient and sustainable manufacturing landscape.
The marvel of precision in manufacturing goes beyond mere numbers; it shapes the fabric of innovation and quality. With technological advancements, we now possess tools that can create intricate designs with unparalleled accuracy. This capability is especially crucial for detailed parts and prototypes, where even a minor deviation can lead to significant functional discrepancies or aesthetic flaws. Industries such as aerospace, automotive, and medical devices rely on this precision not only for performance but also safety, making it an essential cornerstone of their production processes. Moreover, the ability to deliver highly accurate results invites a new era of creativity within design teams. Engineers and designers can explore previously unimaginable concepts without fearing that small imperfections will hinder their vision. They can iterate rapidly, with the assurance that each prototype reflects exact specifications, reducing waste and speeding up time-to-market for innovative solutions. In this landscape, where customization is becoming the norm, precision empowers businesses to set themselves apart by delivering personalized products that meet specific customer needs with impeccable accuracy, transforming challenges into opportunities through meticulous craftsmanship.
Versatility in material handling is a game changer across industries. Imagine a single tool or machine capable of seamlessly transitioning between metals, plastics, and composites, each with its unique properties and challenges. This adaptability not only streamlines manufacturing processes but also fosters innovation by allowing designers to experiment without being limited by the rigidity of traditional machinery. For instance, while metal components may require robust force for shaping, plastic parts often require precision and finesse. Equipment that can handle both adeptly opens up new realms of possibility. Moreover, the ability to work with such diverse materials encourages sustainability practices. In an era where eco-consciousness drives decisions, manufacturers can choose appropriately to minimize waste generated from specialized machines tied to specific materials. By utilizing versatile tools that accommodate various substrates, businesses can embrace recycling initiatives more effectively, transform scrap plastics into new products, or efficiently rework excess metal scraps rather than discard them. This shift toward multipurpose capability not only enhances efficiency but also redefines the interaction between technology and environmental responsibility in our ever-evolving industrial landscape.
Multi-axis control systems redefine the landscape of machining by enabling intricate geometries and complex contours that are often impossible to achieve with conventional machines. The flexibility of 3, 4, or even 5-axis configurations allows manufacturers to push the limits of their designs, circumventing traditional constraints and unlocking new creative possibilities. With each additional axis comes enhanced capability; while a 3-axis machine excels in straight cuts and basic forms, adding a fourth or fifth axis facilitates advanced features like undercuts and complex profiles that significantly improve productivity and reduce tooling time. Moreover, the integration of multi-axis machining into production workflows streamlines processes by minimizing setups and part handling. This reduction not only enhances accuracy, keeping tolerances tighter, but also decreases lead times dramatically. As industries strive for efficiency in a competitive landscape, adopting multi-axis technology is more than just an upgrade; it’s a strategic move toward innovation. By embracing these sophisticated systems, companies position themselves at the forefront of precision engineering, capable of responding rapidly to evolving market demands while ensuring unparalleled quality in their output.
A tool-changing system revolutionizes the way manufacturing environments operate by automating the switch between various tools on machinery. Imagine a complex assembly line where downtime is minimized not just by speed but by seamless transitions; this is precisely what such systems achieve. By integrating advanced robotics and precision engineering, these systems ensure that multiple operations can be conducted with minimal interruption, allowing for greater flexibility in production schedules and enhancing overall workflow efficiency. Moreover, as industries increasingly lean toward customized solutions and just-in-time manufacturing, a robust tool-changing system becomes essential. Instead of dedicating specific machines to singular tasks, manufacturers can now adapt equipment on the fly to meet varying demands without significant setup time or labour costs. This not only maximizes resource utilization but also fosters an environment where innovation thrives, reducing the risk of human error associated with manual tool changes. Ultimately, embracing this technology empowers businesses to maintain a competitive edge in an ever-evolving market landscape.
A tool-changing system revolutionizes the way manufacturing environments operate by automating the switch between various tools on machinery. Imagine a complex assembly line where downtime is minimized not just by speed but by seamless transitions; this is precisely what such systems achieve. By integrating advanced robotics and precision engineering, these systems ensure that multiple operations can be conducted with minimal interruption, allowing for greater flexibility in production schedules and enhancing overall workflow efficiency. Moreover, as industries increasingly lean toward customized solutions and just-in-time manufacturing, a robust tool-changing system becomes essential. Instead of dedicating specific machines to singular tasks, manufacturers can now adapt equipment on the fly to meet varying demands without significant setup time or labor costs. This not only maximizes resource utilization but also fosters an environment where innovation thrives, reducing the risk of human error associated with manual tool changes. Ultimately, embracing this technology empowers businesses to maintain a competitive edge in an ever-evolving market landscape.
Applications Milling CNC Machine
- Prototyping: Rapid development of models and prototypes.
- Production: Mass production of components with consistent quality.
- Custom Parts: Manufacturing custom machine parts or tools.
- Engraving: Creating fine details or patterns.
Tilt table type
VARIAXIS i NEO
Pallet size | Φ27.56" × width 19.69" |
Tool shank | BIG-PLUS No.40 |
Standard Max. spindle speed | 12000 min-1 (rpm) |
Max. workpiece dimension | Φ33.46" × 19.69" |
VARIAXIS i
Pallet size | Φ19.69" × width 15.75" to Φ23.62" × width 19.69" |
Tool shank | BIG-PLUS No.40 / CAT No.40 | Standard Max. spindle speed | 12000 min-1 (rpm) |
Max. workpiece dimension | Φ19.69" × 13.78" to Φ33.46" × 19.69" |
VARIAXIS i NEO
Pallet size | Φ31.5" × width 24.8" |
Tool shank | BIG-PLUS No.50 |
Standard Max. spindle speed | 10000 min-1 (rpm) |
Max. workpiece dimension | Φ33.46" × 19.69" |
VARIAXIS i NEO
Pallet size | Φ41.34" × width 31.5" |
Tool shank | BIG-PLUS No.50 / CAT No.50 |
Standard Max. spindle speed | 12000 min-1 (rpm) |
Max. workpiece dimension | Φ49.21" × 35.43" |
VARIAXIS C
Pallet size | Φ23.62" × width 19.69" |
Tool shank | BIG-PLUS No.40 |
Standard Max. spindle speed | 12000 min-1 (rpm) |
Max. workpiece dimension | 12000 min-1 (rpm) |
VARIAXIS i
Pallet size | Φ19.69" × width 15.75" to Φ23.62" × width 19.69" |
Tool shank | BIG-PLUS No.40 / CAT No.40 | Standard Max. spindle speed | 12000 min-1 (rpm) |
Max. workpiece dimension | Φ19.69" × 13.78" to Φ33.46" × 19.69" |
VARIAXIS j
Pallet size | Φ31.5" × width 24.8" |
Tool shank | BIG-PLUS No.50 |
Standard Max. spindle speed | 10000 min-1 (rpm) |
Max. workpiece dimension | Φ33.46" × 19.69" |
VARIAXIS i NEO
Pallet size | Φ41.34" × width 31.5" |
Tool shank | BIG-PLUS No.50 / CAT No.50 |
Standard Max. spindle speed | 12000 min-1 (rpm) |
Max. workpiece dimension | Φ49.21" × 35.43" |